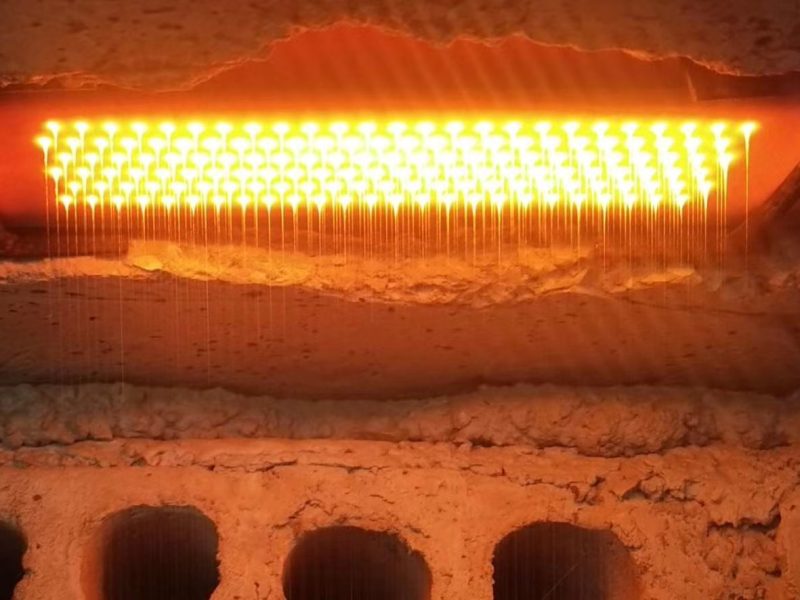
As an important material, glass fiber has a wide range of applications in the industrial field. The mass per unit length of raw silk or yarn, its unit is tex, and the control of tex has a crucial impact on the quality and performance of glass fiber. This article will explore in detail all aspects of glass fiber tex control, including raw material control, melting system development, drawing process, and environmental control.
一. Raw material control
Raw materials are the basis for fiberglass production, and their quality directly affects the tex of the final product. In order to ensure the stability and consistency of raw materials, the following aspects need to be controlled:
1.Choose high-quality raw material suppliers and require them to provide raw materials of stable quality. We proposed the concept of stability, whose component fluctuations need to be controlled within a certain range.
2.Conduct strict testing of raw materials, including chemical composition, particle size distribution and other indicators.
3.Ensure that raw materials are stored in good conditions to avoid moisture, contamination, etc. Because some raw materials absorb moisture significantly, the requirements during transportation, packaging, and cutting are different. Such as quicklime, soda ash, kaolin, etc.
4.Classify and manage different batches of raw materials to ensure consistency in the production process.
二. Formulation of melting system
The melting system is one of the key factors affecting glass fiber tex. A reasonable melting system should consider the following points:
1.Precisely control the temperature of the furnace to ensure the uniformity and stability of the melt. (The melting temperature should be appropriate according to the characteristics of the material itself. There is no need to pursue the temperature system of other factories too much, but the crystallization temperature still needs to be paid attention to)
2.Optimize melting time to obtain appropriate glass viscosity. (The five stages of melting will be discussed in detail later)
3.Reasonably adjust the ratio of fuel and combustion accelerant to improve melting efficiency. (The overall kiln adopts weak oxidizing properties)
4.Pay attention to the flow properties of the melt to avoid unevenness.
三. Wire drawing process
The drawing process is of great significance to the control of glass fiber tex. Here are some key points:
1.Choose appropriate wire drawing equipment to ensure the stability and accuracy of the equipment.
2.Control the drawing speed to achieve the desired tex. (Consider linear speed, rotational speed, runout, etc.)
3.Ensure the temperature is stable during the drawing process to avoid temperature fluctuations affecting tex.
4.Optimize the design and use of drawing leakage plates to improve drawing quality.
四. Environmental control
Environmental factors will also have an impact on the tex of glass fiber, so effective control is required:
1.Keep the production workshop clean and reduce interference from dust and impurities.
2.Control the temperature and humidity of the workshop to create a suitable production environment. (The temperature of the drain panel control room is also a point of concern)
3.Avoid the influence of external vibration and interference on the drawing process.
To sum up, the control of glass fiber tex requires comprehensive consideration of raw material control, melting system formulation, drawing process and environmental control. Only with strict control and management in all aspects can high-quality fiberglass products with stable tex be produced.
Recent Comments