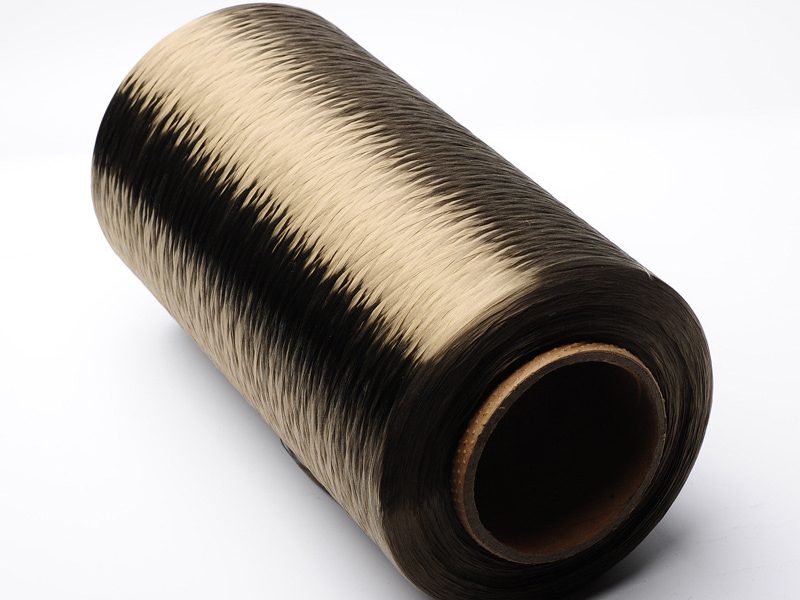
Basalt fiber is a continuous fiber made of natural basalt stone as the main raw material. It is melted at 1450-1500°C and drawn at high speed through a platinum-rhodium alloy drawing drain plate. The color is generally brown and has a metallic luster. It is composed of oxides such as silicon dioxide, aluminum oxide, calcium oxide, magnesium oxide, iron oxide and titanium dioxide. Basalt fiber has many excellent properties such as high strength, electrical insulation, corrosion resistance, high temperature resistance, and anti-aging. It also has good compatibility with the environment and does not produce secondary pollution. Therefore, it is a truly green, high-performance new environmentally friendly material.
If you understand the production process of basalt fiber, you will definitely be shocked by its “hard core”: natural basalt stone formed by volcanic eruptions is used as raw material, crushed and put into a furnace, and heated to a molten state at 1450~1500℃ , quickly drawn through a platinum-rhodium alloy drawing leakage plate, this is how basalt fiber is produced. In short, the process of making basalt fiber is to “draw” hard volcanic basalt rock into filaments at high temperatures. The diameter of basalt fibers produced by existing processes can reach 6~13μm, which is thinner than a human hair.
The production process is as shown below.
As an amorphous inorganic silicate material, basalt fiber has a short production period, simple process, no industrial wastewater and waste gas, and high added value. It is known as the “green new material” in the 21st century. And because its color is golden brown, the process of producing basalt fiber is called “turning stone into gold”.
Excellent properties of basalt fiber
Purely natural continuous basalt fiber has a golden color, a smooth cylinder in appearance, and a complete circle in cross-section. Basalt fiber has high density and hardness, so it has excellent wear resistance and tensile strengthening properties. Basalt fiber is an amorphous material. Its operating temperature is generally between -269~700℃ (softening point is 960℃). It is acid and alkali resistant, has strong UV resistance, low hygroscopicity and good environmental resistance. In addition, it has the advantages of good insulation, high-temperature filtration, radiation resistance and good wave transmittance, thermal vibration stability, environmental cleanliness, and an excellent ratio of structural performance to structural quality.
1. Sufficient raw materials Basalt fiber is made by melting and drawing basalt ore. The reserves of basalt ore on the earth and the moon are quite objective, and the cost of raw materials is relatively low.
2. Environmentally friendly material Basalt ore is a natural material. No boron or other alkali metal oxides are emitted during its production process, so no harmful substances are precipitated in the smoke and it does not cause pollution to the atmosphere. Moreover, the product has a long service life, so it is a new green active environmentally friendly material with low cost, high performance and ideal cleanliness.
3. The working temperature range of high temperature and water resistant continuous basalt fiber is generally -269~700℃ (softening point is 960℃), while that of glass fiber is -60~450℃, and the maximum operating temperature of carbon fiber can only reach 500℃. In particular, when basalt fiber works at 600°C, its post-break strength can still maintain 80% of its original strength; when it works at 860°C, it will not shrink. Even mineral wool with excellent temperature resistance can only maintain its post-break strength at 860°C. 50%-60%, glass wool is completely destroyed. Carbon fiber produces CO and CO2 at approximately 300°C. Basalt fiber can maintain high strength under the action of hot water at 70°C, and basalt fiber may lose part of its strength after 1200 hours.
4. Good chemical stability and corrosion resistance. Continuous basalt fiber contains components such as K2O, MgO) and TiO2, and these components are extremely beneficial and play a very important role in improving the chemical corrosion resistance and waterproof performance of the fiber. Compared with the chemical stability of glass fiber, it has more advantages, especially in alkaline and acidic media. Basalt fiber can also maintain higher resistance in alkaline media such as saturated Ca(OH)2 solution and cement. Alkaline corrosion properties.
5. High elastic modulus and tensile strength The elastic modulus of basalt fiber is: 9100 kg/mm-11000 kg/mm, which is higher than alkali-free glass fiber, asbestos, aramid fiber, polypropylene fiber and silicon fiber. The tensile strength of basalt fiber is 3800-4800 MPa, which is higher than large tow carbon fiber, aramid fiber, PBI fiber, steel fiber, boron fiber and alumina fiber, and is equivalent to S glass fiber. The density of basalt fiber is 2.65-3. 00 g/cm3, and its hardness is very high, with Mohs hardness of 5-9 degrees, so it has excellent wear resistance and tensile strengthening properties. Its mechanical strength far exceeds that of natural fibers and synthetic fibers, so it is an ideal reinforcing material. Its excellent mechanical properties are at the forefront of the four high-performance fibers.
6. Excellent sound insulation performance. Continuous basalt fiber has excellent sound insulation and sound absorption properties. It can be known from the sound absorption coefficient of the fiber at different frequencies. As the frequency increases, its sound absorption coefficient increases significantly. For example, sound-absorbing materials made of basalt fiber with a diameter of 1-3 μm (density 15 kg/m3, thickness 30mm) are used. Under the audio frequency conditions of 100~300 Hz, 400~900 Hz and 1200~7 000 HZ, the fiber The sound absorption coefficients of the materials are 0. 05~0.15, 0. 22~0. 75 and 0.85~0.93 respectively.
7. Outstanding dielectric properties The volume resistivity of continuous basalt fiber is one order of magnitude higher than that of E-glass fiber and has excellent dielectric properties. Although the basalt ore contains a conductive oxide with a mass fraction of nearly 0.2, after special surface treatment with a special sizing agent, the dielectric loss tangent of the basalt fiber is 50% lower than that of glass fiber, and the volume resistivity of the fiber is also higher than that of glass fiber
8. Natural silicate has good dispersion with cement and concrete, strong binding force, consistent coefficient of thermal expansion and contraction, and good weather resistance.
9. Lower hygroscopicity: The hygroscopicity of basalt fiber is less than 0.1%, which is lower than aramid fiber, rock wool and asbestos.
10. Lower thermal conductivity coefficient The thermal conductivity coefficient of basalt fiber is 0.031 W/m·K – 0.038 W/m·K, which is lower than aramid fiber, aluminum silicate fiber, alkali-free glass fiber, rock wool, silicon fiber, Carbon fiber and stainless steel.
Applications of basalt fiber
Basalt fiber has the characteristics of high strength and high and low temperature resistance, which is very consistent with the surface material requirements of aircraft and missiles. At the same time, it has the characteristics of wave absorption and magnetic permeability, which can achieve radar invisibility. Therefore, basalt carbon fiber can partially replace carbon fiber in stealth aircraft and missiles.
Current body armor usually uses ultra-high molecular weight polyethylene fiber, which has low heat resistance. The strength and modulus will be reduced when the warhead is burned at high temperatures, affecting the bulletproof effect. In contrast, basalt fiber has strong high temperature resistance and does not have this problem.
Basalt fiber has low thermal conductivity, good flame retardant properties, and an operating temperature range of -269°C to 700°C, making it resistant to both high and low temperatures. Meet the stringent requirements for materials in the aerospace field. Most of Russia’s aerospace materials are made of this material.
Basalt fiber has the advantages of high tensile strength, good mechanical properties, high temperature resistance, UV protection, acid and alkali resistance, salt resistance, and anti-aging. Compared with other fibers, its comprehensive performance is better and it also meets the material requirements in the field of road engineering. Therefore, in recent years, more and more basalt fiber products have been used in road engineering.
Heat insulation, temperature resistance and fire protection fields
Basalt fiber has high temperature resistance and can be woven into fireproof cloth and used in some fire protection fields. It can also be woven into high-temperature filter bags for high-temperature filtration and dust removal. In addition, it can also be made into needle felt and used in some thermal insulation fields.
construction field
Taking advantage of the excellent corrosion resistance of basalt fiber, it can be compounded with vinyl or epoxy resin through pultrusion, winding and other processes to make new building materials. This material has high strength, excellent acid resistance and corrosion resistance, and can replace some steel bars in civil engineering. Moreover, the expansion coefficient of basalt fiber is similar to that of concrete, and there will be no large temperature stress between the two.
Automotive field
Basalt fiber has a stable friction coefficient and can be used in some friction reinforcement materials, such as brake pads. Due to its high sound absorption coefficient, it can be used in some interior parts to achieve sound insulation and noise reduction.
Petrochemical field
The corrosion resistance of basalt fiber gives it unique advantages in the petrochemical industry. Commonly used are wound high-pressure pipes combined with epoxy resin, which have dual effects of insulation and anti-corrosion.
Recent Comments