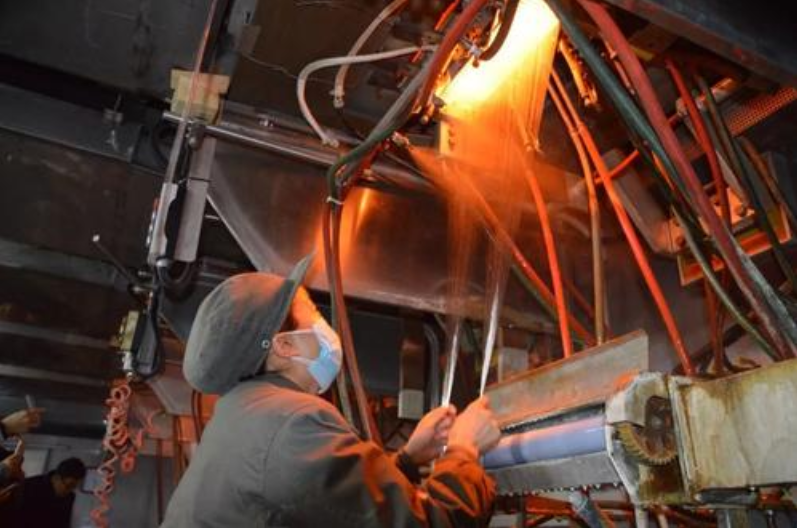
Wetting agent is a system composed of a variety of organic and inorganic substances. From the appearance, it can be a solution, emulsion, thixotropic colloid or paste. Sizing agents generally consist of film-forming agents, coupling agents, lubricants, additives and auxiliary components.
(1) Film-forming agent. The film-forming agent is the adhesive component in the sizing agent. It is the main component that realizes the bundling of single filaments and maintains the integrity of the original filaments. It determines the stiffness and softness of the original filaments to meet the needs of different types of glass fiber products. Require. This component is used in the largest amount in the sizing agent formula, accounting for 2%-15%, and has an important impact on the performance and function of the sizing agent. It is the most critical component of the sizing agent. Different formulas require different types of raw materials. Sometimes more than two film-forming agents are often used to achieve the effect set by the sizing agent formula.
(2) Coupling agent. The use of coupling agents is one of the characteristics of enhanced wetting agents. Through its own various reactive groups, it combines glass fiber with high molecular polymers such as resin, which acts as a bridge to achieve good interface bonding between inorganic substances and organic substances, so that glass fiber reinforced materials can obtain satisfactory results. Apply effects. Different coupling agents have different effects on the strength of glass fiber composite materials. It is necessary to correctly select the type of coupling agent based on the resin matrix material and its curing agent. Usually the coupling agent is used in the sizing agent formula at a dosage of 0.2%-1.2%.
(3) Lubricant. Lubricant refers to a substance that lubricates the surface of glass fiber and reduces wear in the wet state (during wire drawing process) and dry state (during raw silk recombination and textile processing). Its dosage in the composition of the sizing agent is generally 0-5%. The types and dosages of lubricants vary greatly among sizing agents for different uses.
(4) Antistatic agent. Antistatic agents can effectively reduce the electrostatic effect of glass fibers during processing and use, and their use effect is particularly significant among glass fiber sizing agents for chopped processing. The main principle of antistatic is to reduce the friction coefficient and form a conductive channel.
(5) Auxiliary ingredients
1. Wetting agent. A wetting agent is a surface-active substance. It can reduce the surface tension of the sizing system, making it easier for the sizing to wet the surface of the glass fiber and achieve the effect of evenly coating the glass fiber.
2. pH regulator. The sizing system is generally neutral or weakly acidic, and pH regulators are mostly used to adjust the stability of the sizing system and ensure the best use of the coupling agent. Commonly used pH regulators include formic acid, acetic acid, citric acid, oxalic acid, ammonia, organic amines, etc. Considering that the sizing agent is in direct contact with people and machinery, the pH value in the general formula is in the range of 4-7. For individual sizing agents, the composition The film emulsion can be used stably or reach the required viscosity only under alkaline conditions. The pH value of the sizing agent system is controlled at 8-11, but this is relatively rare.
3. Plasticizer. Substances added to the sizing system in order to improve the flexibility of the film-forming agent. When preparing the sizing agent, it can sometimes be added directly to the film-forming agent. Commonly used plasticizers include dibutyl phthalate, dioctyl phthalate, tributyl phosphate, etc. The use of monofilament plasticizers sometimes affects the wetability of the yarn and should only be used when the performance provided by the sizing system does not meet the needs.
4. Cross-linking agent. After the cross-linking agent is added to the sizing system, during the drying process of the raw silk, it will produce a cross-linking reaction with a certain film-forming agent in the sizing agent, transforming the original linear molecular structure into a three-dimensional network structure, improving the hardness of the film, and improving the film’s hardness. Improving the performance of hard yarns is very beneficial, but at the same time it will cause problems such as difficulty in yarn penetration and poor stability of the sizing agent.
5. Preservatives and fungicides. When the sizing agent formula contains starch, gelatin, hydrogenated vegetable oil, stearic acid or oleic acid lubricants and other ingredients that are prone to decay, mold, and deterioration, preservatives or fungicides need to be used.
6. Defoaming agent. The film-forming agent emulsion and lubricant in the sizing agent contain certain surface active ingredients, which are prone to foam during mixing and use, causing inconvenience to production and application. Sometimes it is necessary to add a defoaming agent to eliminate foam. Defoaming agents are generally organosilicon compounds, which are usually sprayed on the surface in small amounts after the sizing agent is prepared.
Recent Comments